Industrial Engineer
Poway, California
Overview
General Atomics pioneers technologies with the potential to change the world. Behind a talented global team of engineers, GA delivers safe, sustainable, and economical solutions to meet growing global demands. Our Engineers have an opportunity to work on first of a kind product lines within an incredible, dynamic environment.
Engineering positions typically require a bachelor’s degree, master’s degree or PhD in engineering or a related technical discipline from an accredited institution and progressive engineering experience. Candidates from mechanical, electrical, and aerospace engineering backgrounds must know the fundamentals of engineering system developments, requirements, testing, and integration before getting to the final stages of customer interface and project management.
Schedule: Full-Time Salary
Job Level: Mid-Level (3-7 years)
Travel: 0 - 25
Success Profile
What makes a successful Industrial Engineer at General Atomics? Check out the top traits we’re looking for and see if you have the right mix.
- Analytical
- Collaborative
- Inventive
- Problem Solver
- Team Player
- Creative
Job Summary General Atomics Aeronautical Systems, Inc. (GA-ASI), an affiliate of General Atomics, is a world leader in proven, reliable remotely piloted aircraft and tactical reconnaissance radars, as well as advanced high-resolution surveillance systems.
We currently have an exciting opportunity for an Industrial Engineer within our ASI Division.
DUTIES AND RESPONSIBILITIES:
- Responsible for understanding the integration of manpower, manufacturing space, material, equipment, etc. for a manufacturing system, and use lean tools to sustain, monitor, and improve the state of the system.
- Identify systemic problems through root cause analysis. Implement corrective and/or preventive action to improve safety, quality, cost, and delivery.
- Initiate and lead lean manufacturing process improvement projects via Kaizen event facilitation and/or general floor support.
- Support and collaborate with shop floor technicians and manufacturing support teams to solve problems.
- Promote and sustain lean culture through employee empowerment and training of lean tools and principles.
- Specify and implement equipment and processes including efficient layout and optimization of material and information flows.
- Establish and maintain labor standards, lead times and capacities/capabilities for manufacturing and ancillary processes.
- Establish and maintain work instructions and other documentation associated with manufacturing and ancillary processes.
- Develop meaningful process metrics and support the enterprise in making data driven decisions.
- Clearly and effectively communicate both verbally and in written form to both technical and non-technical audiences, especially regarding manufacturing processes, engineering issues and proposed changes, and quality issues and dispositions.
Job Qualifications:
- Typically requires a bachelors degree, masters degree or PhD in engineering or a related technical discipline from an accredited institution and progressive engineering experience as follows; four or more years of experience with a bachelors degree or two or more years of experience with a masters degree. May substitute equivalent engineering experience in lieu of education.
- Experience with Engineering change processes, from requests through implementation is required.
- Experience leading cross functional teams through problem solving and project execution.
- Expertise in complex assembly methods and processes (aerospace and composites a plus).
- Experience in project management and knowledge of Project Management Body of Knowledge a plus
- Experience with Drawings and engineering/manufacturing bill of materials is required.
- Experience with Lean/Six Sigma Manufacturing methodologies for waste reduction and their application in a manufacturing environment is required.
- Proficiency with Microsoft Office Word, Excel, Outlook and PowerPoint.
- Knowledge of ERP systems (SAP desirable).
- Basic CAD design experience (floor layout and small tooling preferred).
- Materials management (warehousing, transportation, logistics) experience desirable.
- Must have a general understanding of engineering concepts, principles, and theory with technical experience demonstrating the application of those concepts while ensuring safety and regulatory compliance.
- Must possess the ability to understand new concepts quickly and apply them accurately throughout an evolving environment and organize work assignments to meet established timetables.
- Good communication, computer, documentation, presentation, and interpersonal skills are required, as well as the ability to work both independently and as part of a team.
- Must be able to work extended hours as required.
Salary:$81,080 - $141,650
Benefits
-
Healthcare
-
Pension, 401(k)/Retirement Plans
-
Competitive Pay
-
Multiple product lines means a variety of work
-
Paid Time Off
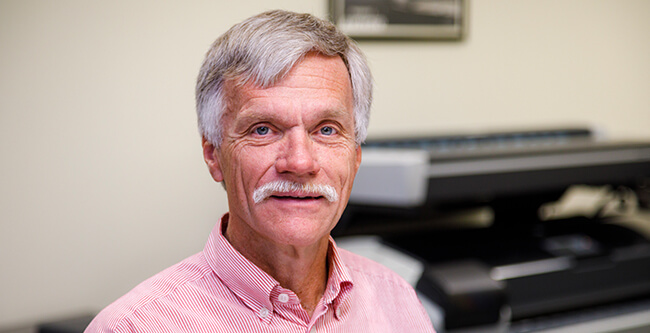
“The company is growing, has a very good reputation and had open positions in my area of expertise (aircraft design/design methodology development).”– Peter, Senior Staff Engineer
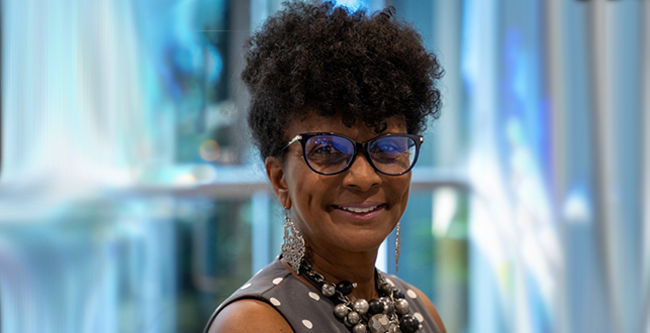
“We don't ascribe to quotas; we do ascribe to securing the BEST talent to enrich our culture toward healthy diversification and active/viable community service. We are STEM advocates.”– Debra, CSSBB: Staff Engineer
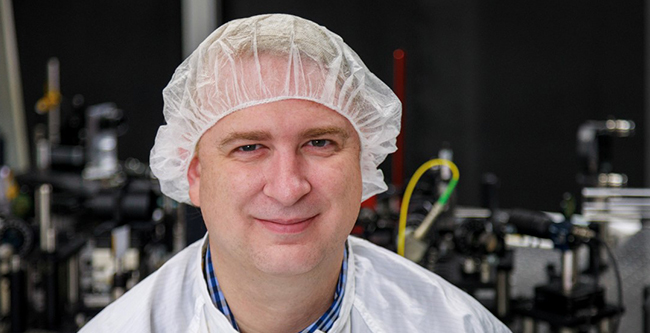
“Every day is different, with different problems to solve and many programs to support. I am a problem solver and have always been motivated by the tough questions.”– Scott, Laser Scientist
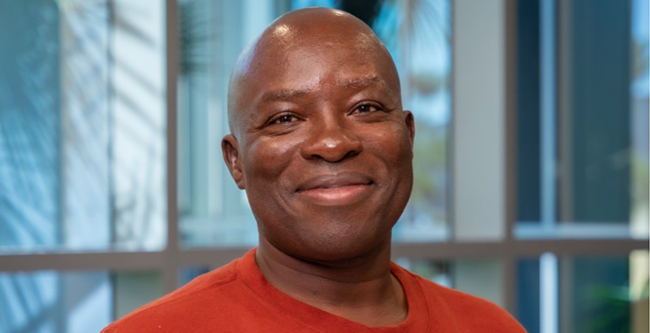
“I work in the Components Engineering and Obsolescence Management Dept. Our efforts are saving General Atomics several millions of dollars by proactively leading and informing the company of all these decisions which significantly impact production, sustainment and new designs.”– John, Staff Engineer
News
-
Featured Jobs
- Project Engineer, Taiwan Program Poway, California
- In-House Counsel San Diego, California
- Legal Assistant San Diego, California
- Structural Test Engineering Supervisor Adelanto, California
You have not recently viewed any jobs.
You have no saved jobs.
-
Featured Jobs
- Project Engineer, Taiwan Program Poway, California
- In-House Counsel San Diego, California
- Legal Assistant San Diego, California
- Structural Test Engineering Supervisor Adelanto, California
You have not recently viewed any jobs.
You have no saved jobs.
-
Featured Jobs
- Project Engineer, Taiwan Program Poway, California
- In-House Counsel San Diego, California
- Legal Assistant San Diego, California
- Structural Test Engineering Supervisor Adelanto, California
You have not recently viewed any jobs.
You have no saved jobs.